The culprit is not in the electrical system nor in the robust starter motor. The problem is with the clutch system that transfers the energy and motion of the electric starting motor to the crankshaft. The 450 is a healthy engine with a lot of moving parts. Combine the engine compression with the drag of those rotating parts and the 450 presents a substantial load for the Electric Starting system to handle. Press the starter button and the solenoid brings on all of the battery’s amperage to the heavy duty starting motor. The starter clutch engages when rotated and the slack in the starter chain slaps the crankshaft into rotation. The combination of high torque, slack in the chain, and a heavy rotational load “hammers” on and will eventually overwhelm the 3 small, under-sized 6mm machine screws that hold the clutch hub to the alternator rotor.
Diagnosing and Re-Engineering The 1965-1974 Honda 450 Electric Starter
Many of us hold Honda’s 444cc DOHC Twins built between 1965~1974 sacred and believe them to be among the true engineering marvels of their time. There is however one dark, dirty little secret that you don’t hear much about. The Electric Starter Systems were under-built and would often fail in just a few thousand miles.
While these vertical twins had some very impressive technology for their day, there is one area of engineering where Honda went wrong – bad wrong. The Starter Clutch was poorly designed. I am 4 for 4 with failures on their starter clutches. That’s the dirty little secret that I learned about the hard way. Now, I don’t consider myself lucky or unlucky, but with those odds in mind, I do believe every Honda CB450 and CL450 electric starting system would and will fail sooner than later. In my most recent experience, the failure lead to broken parts in the transmission and those broken parts left the bike’s owner stranded beside the road at night. The mileage for the 4 different “broken bikes” was 1,362 miles, 4,060 miles, 6,287 miles, and that most recent one with only 7,311 miles.
Thank you for Following
Related Articles
The three-wheeler electrifying the Arima hot spring tourism trade
The Motorcycle Mechanics Institute Does Vintage Too
Harley-Davidson Street 750’s Brakes Completely Fail In Magazine Test
Zero Motorcycles ZeroCast: Z-Force Motors With Ryan Biffard – Webinar
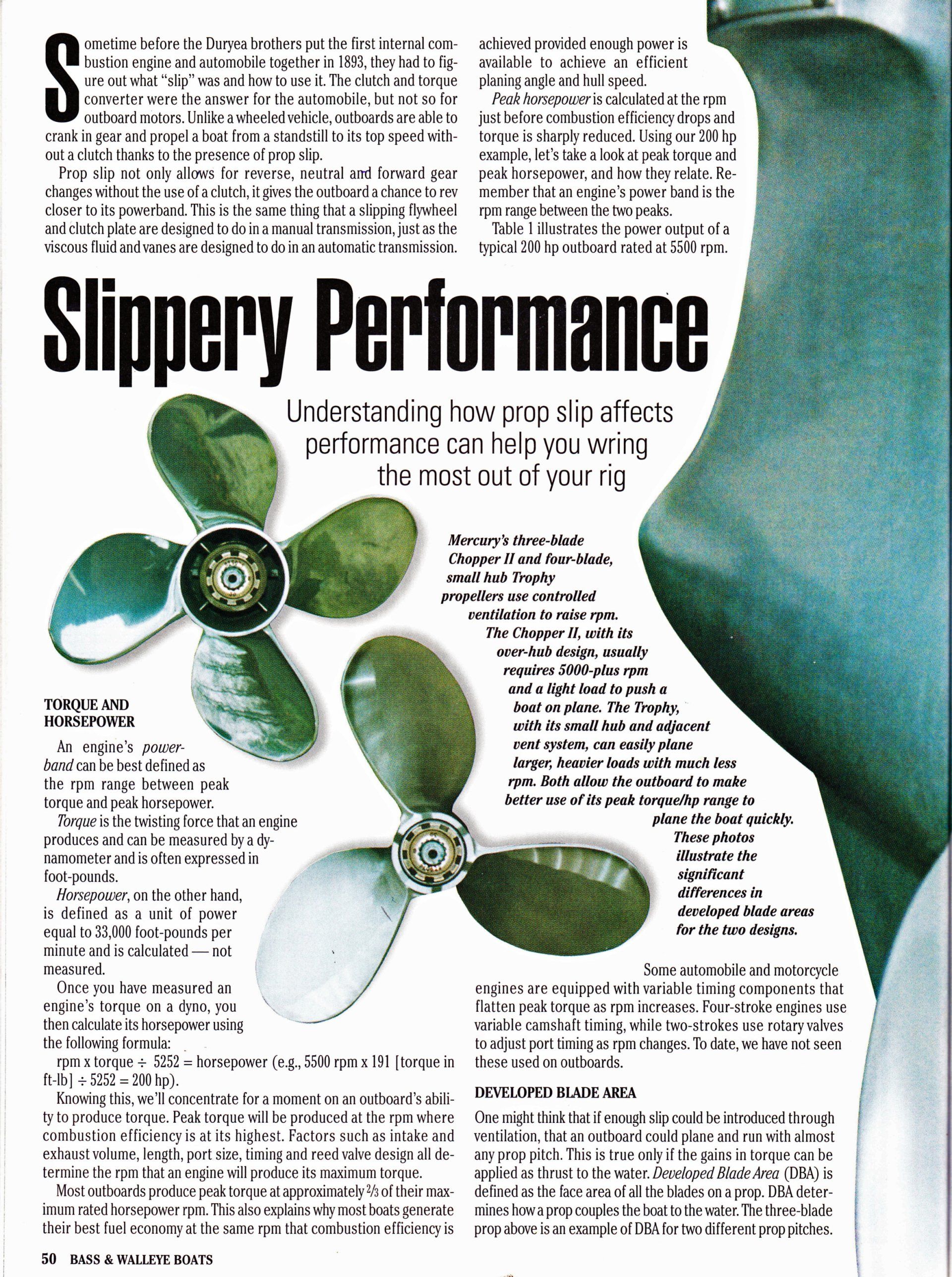
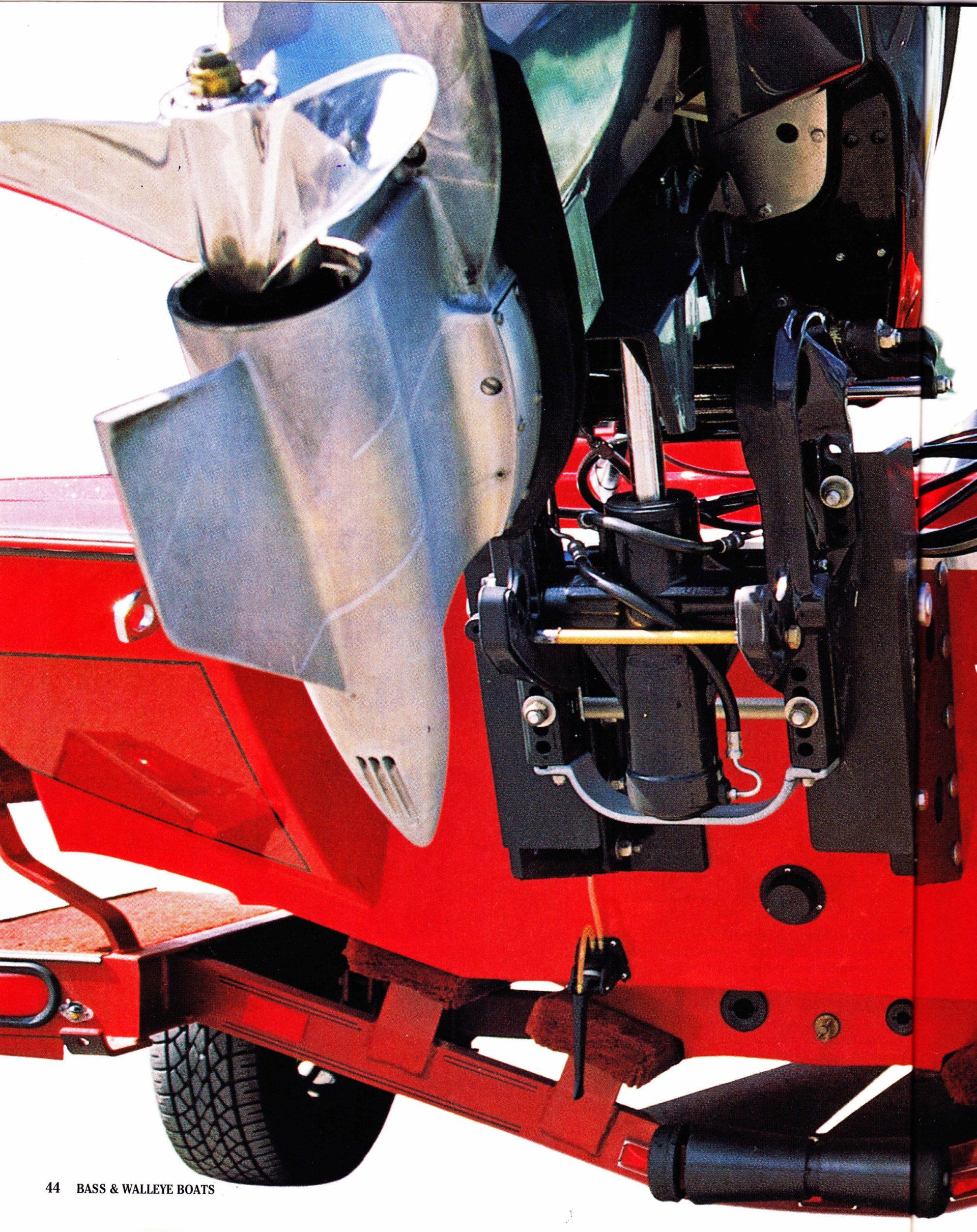
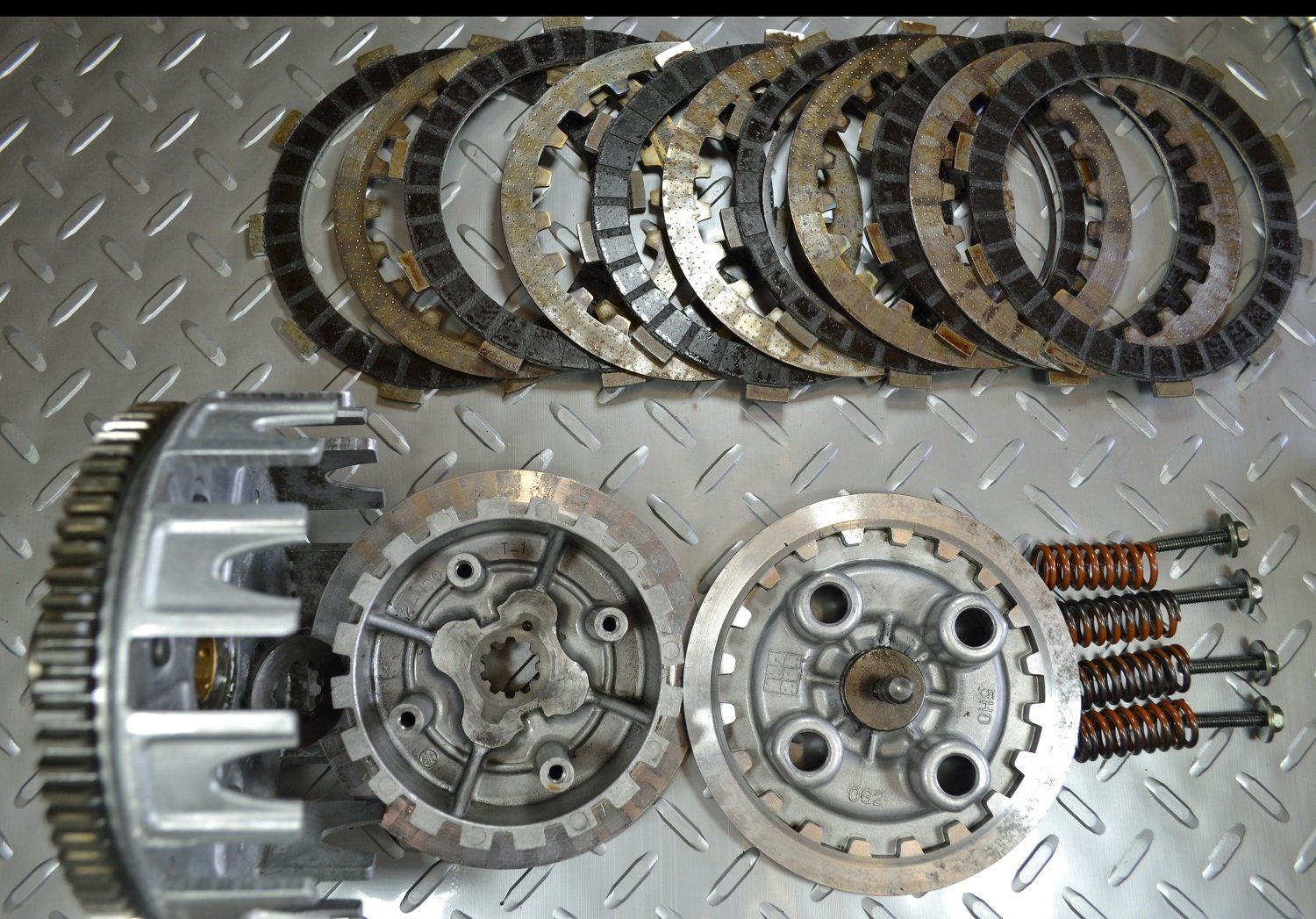
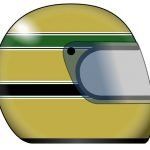